Laser cutting is a precise and efficient process used in various industries, including manufacturing, automotive, and aerospace. A critical component of this process is the use of gas to enhance the quality of the cuts and extend the lifespan of the laser equipment. Setting up a nitrogen generator for laser cutting can significantly reduce operating costs and improve productivity by providing a consistent and high-purity supply of gas on-site.
Using a nitrogen generator for laser cutting offers numerous benefits. This setup ensures that you have a continuous supply without the need to rely on external suppliers, which can be costly and inconvenient. In this guide, we will walk you through the steps necessary to set up a generator for laser cutting, ensuring optimal performance and efficiency.
Understanding the Basics of Nitrogen Generators

A generator produces gas from compressed air through processes like Pressure Swing Adsorption (PSA) or membrane technology. PSA is the most common method used in industrial applications due to its efficiency and reliability. This technology uses a material called a carbon molecular sieve to separate gas molecules from other gases in the air, producing high-purity gas suitable for laser cutting.
Assessing Your Requirements
Before setting up a generator, it is crucial to determine the amount of gas your laser cutting operations require. This depends on several factors, including the type and thickness of materials being cut, the cutting speed, and the frequency of operations. Consult with your laser cutting equipment manufacturer for specific requirements and recommendations.
Selecting the Right Nitrogen Generator
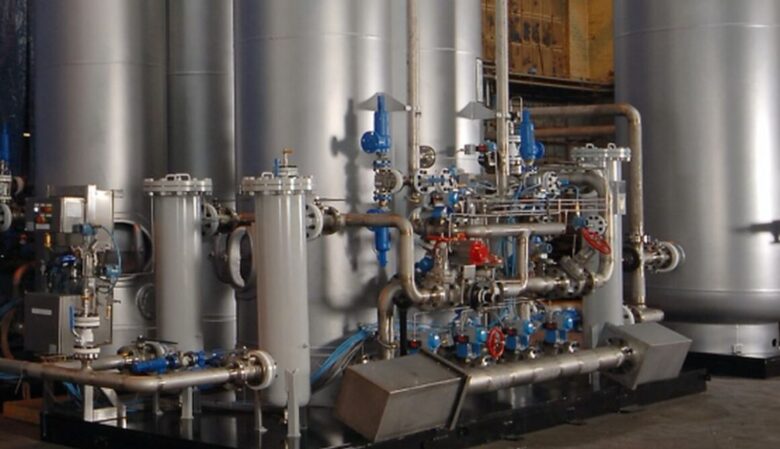
Choosing the appropriate generator for laser cutting involves considering factors such as gas purity, flow rate, and pressure requirements. Laser cutting typically requires high-purity gas, usually 99.99% or higher, to ensure clean cuts and prevent oxidation. The flow rate and pressure requirements will vary based on your specific cutting operations.
Installation Process
- Site Preparation: Ensure the installation area is clean, well-ventilated, and has sufficient space for the generator and associated equipment. The area should be free from dust, moisture, and extreme temperatures to maintain optimal performance.
- Electrical Connections: Connect the generator to a reliable power source. Follow the manufacturer’s guidelines for electrical requirements, ensuring that the power supply is stable and sufficient to handle the generator’s load.
- Compressed Air Supply: The generator requires a source of compressed air. Install an air compressor if you do not already have one. The compressor should be capable of delivering the required pressure and flow rate for the generator.
- Piping and Fittings: Use appropriate piping and fittings to connect the compressed air supply to the generator. Ensure all connections are secure and leak-free. It is essential to use high-quality materials to prevent contamination and maintain gas purity.
- Cooling and Ventilation: Generators produce heat during operation. Ensure proper cooling and ventilation to prevent overheating and ensure efficient performance. Install fans or cooling systems as needed based on the manufacturer’s recommendations.
System Calibration and Testing
Once the generator is installed, it is crucial to calibrate the system and perform thorough testing to ensure optimal performance. This includes checking the gas purity, flow rate, and pressure to meet the requirements of your laser cutting operations. Regular calibration and maintenance are necessary to maintain consistent performance and extend the lifespan of the equipment.
Integration with Laser Cutting Equipment
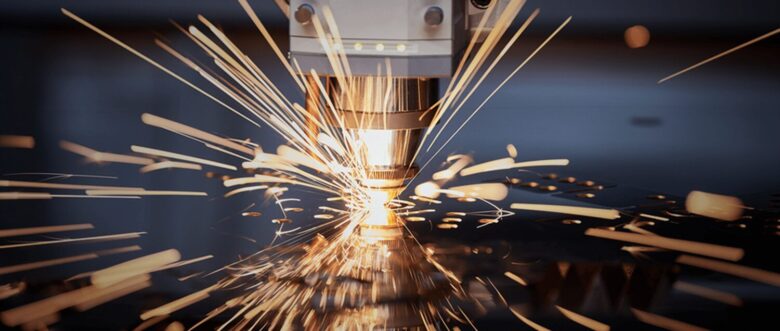
Integrate the generator with your laser cutting equipment by connecting the gas output to the laser cutter’s gas inlet. Ensure that the connections are secure and that the gas supply meets the required purity and pressure specifications. It may be necessary to adjust the settings on your laser cutting equipment to optimize the use of gas for cutting operations.
Maintenance and Troubleshooting
Regular maintenance of the generator is essential to ensure continuous and efficient operation. This includes replacing filters, checking for leaks, and monitoring the performance of the generator. Establish a maintenance schedule based on the manufacturer’s recommendations and adhere to it strictly.
Benefits of Using a Nitrogen Generator for Laser Cutting
Using a generator for laser cutting provides several advantages:
- Cost Savings: On-site gas generation reduces the reliance on external suppliers, leading to significant cost savings over time.
- Consistency: A generator provides a continuous and reliable supply of high-purity gas, ensuring consistent cutting quality.
- Convenience: Having an on-site gas supply eliminates the need for frequent deliveries and storage of gas cylinders.
- Environmental Impact: On-site gas generation reduces the carbon footprint associated with the transportation and production of gas.
Cost Analysis and Budgeting
Setting up a generator involves an initial investment, but the long-term cost savings make it a worthwhile expenditure. When planning your budget, consider the costs of purchasing and installing the generator, air compressor, piping, and any necessary cooling or ventilation systems. Additionally, factor in the ongoing maintenance costs and potential energy savings from having an on-site gas supply.
Ensuring Compliance with Safety Standards
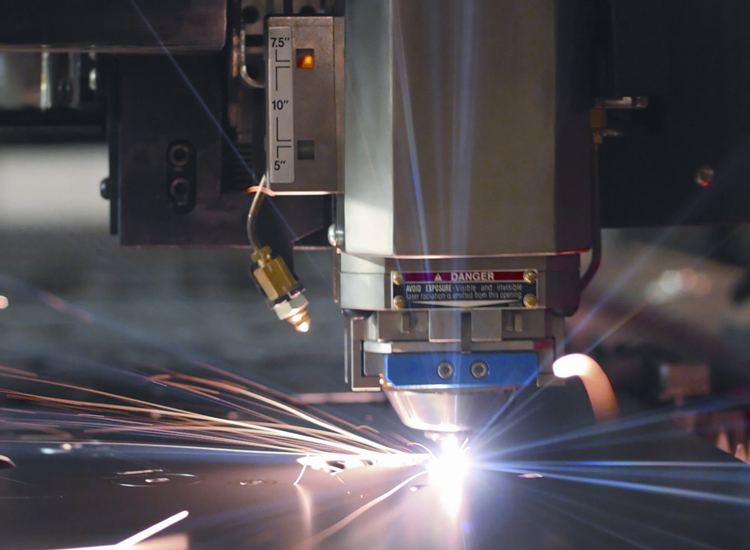
Safety is paramount when dealing with industrial gases. Ensure that your generator setup complies with all relevant safety standards and regulations. This includes proper installation, regular maintenance, and adequate training for personnel handling the equipment. Install safety devices such as pressure relief valves and gas detectors to prevent accidents and ensure a safe working environment.
Future-Proofing Your Setup
As your business grows, your gas requirements may increase. When selecting and installing a generator, consider future expansion and scalability. Choose a generator that can be easily upgraded or expanded to meet increased demand. This will save you time and money in the long run by avoiding the need for a complete overhaul of your gas supply system.
Common Issues and Solutions
Even with regular maintenance, generators can encounter issues. Common problems include reduced gas purity, low flow rates, and equipment malfunctions. Understanding these issues and knowing how to address them can minimize downtime and maintain optimal performance. Regularly inspect and replace filters, check for leaks, and monitor the performance of the generator to catch any issues early.
Training and Operational Best Practices
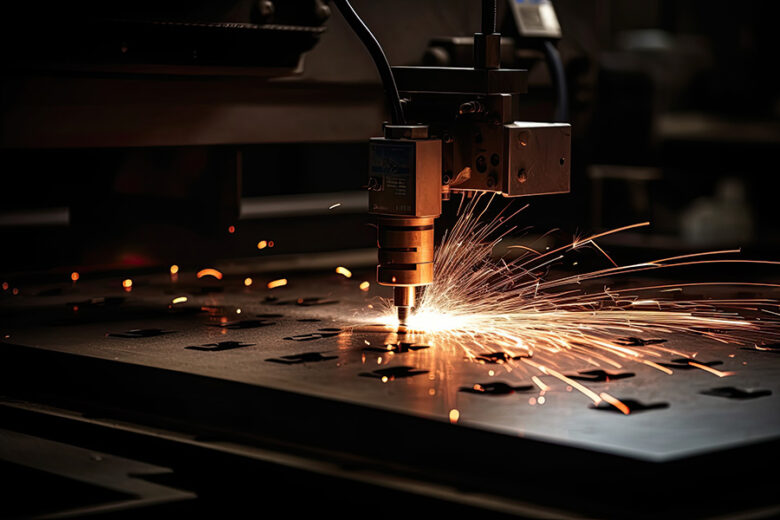
Proper training for your staff is essential to ensure the safe and efficient operation of the generator. Provide comprehensive training on the setup, operation, maintenance, and troubleshooting of the equipment. Establish standard operating procedures and best practices to ensure consistency and reliability in your gas supply.
Environmental Considerations
Using a generator for laser cutting has environmental benefits. On-site gas generation reduces the need for transportation and storage of gas cylinders, which in turn reduces greenhouse gas emissions. Additionally, modern generators are designed to be energy-efficient, further minimizing their environmental impact. By adopting sustainable practices, you can contribute to environmental conservation while enhancing your operational efficiency.
Conclusion
Setting up a generator for laser cutting involves several steps, from understanding the basics of gas generation to installation, calibration, and maintenance. By following the guidelines outlined in this article, you can ensure a successful and efficient setup that enhances the performance and cost-effectiveness of your laser cutting operations.